この記事では、製造業のサプライチェーンマネジメント(SCM)、特に資材調達・購買部におけるBCP(Business Continuity Plan)についてまとめていきます。
・BCPって何のこと?
・なぜBCPが必要なの?
・今後はどんなBCPが必要だろうか?
こんな疑問を解決します。
・BCPの歴史と目的
・BCPの概要と問題点
・これまでに行ってきたBCPの実例とこれから必要なBCPも紹介
本記事は25年間製造業の調達資材購買部で働いている経験から書いています。
東日本大震災以前は、BCPは一般的な概念ではありませんでしたが、現在は製造業にとって必須な考え方となっています。
記事を読むことで「調達・購買部におけるBCPとは何か?」について理解できます。
転職活動での不意の質問にも、実体験のように答えられるようになりますよ。
記事の信頼性として、わたしの市場価値は以下の通り。
転職者に必須のMIIDAS(ミイダス)での市場価値診断では969社からのオファーと、平均の提案年収は678万円でした。
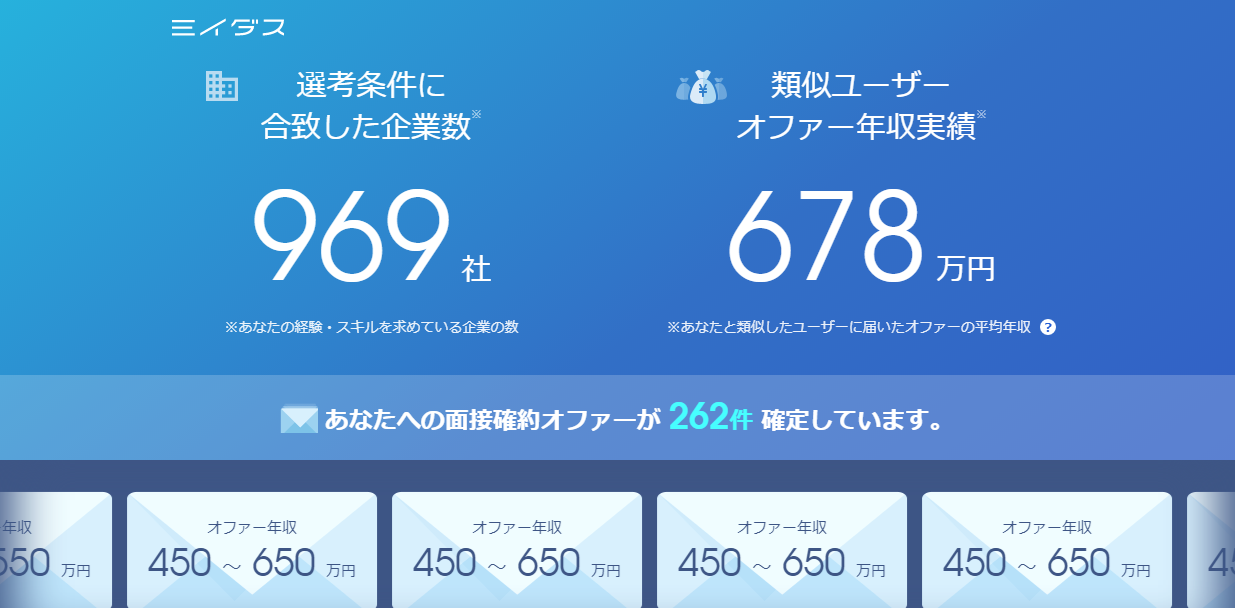
では始めていきましょう。
製造業のサプライチェーンBCP対応とは?現役の調達購買部長が解説

まずは、BCPの言葉の意味について説明します。
BCPとは Business Continuity Planの略で、日本語では「事業継続計画」です。
「事業継続計画」とは、企業が社会的責任を認識し、自然災害や事故などの有事の際にも商品やサービスの供給を中断しないために、事前に策定するものです。
調達資材購買部でのBCPとは、「有事の際にも調達品を確保するための取り組み」になります。
具体的には以下のことを目的とします。
・自然災害・事故などの有事における供給責任を果たすこと
・事前に調達リスクの特定とリスクを減らす管理をしておくこと
地震や、台風、事故など、取引先に何かあった場合、購入品を確保することは、企業の責任として、とても大事なことですから、BCPは調達資材購買部門の非常に重要な仕事です。
BCPの成り立ちの歴史は、つい最近から
実はBCPという概念が一般的になったのは、つい最近のことです。
少なくとも、1995年の阪神・淡路大震災のときには、BCPという概念が一般的になることはありませんでした。
BCPの概念が広まったのは、2011年に起きた2つの大きな災害が原因です。
・東日本大震災
・タイの洪水
東日本大震災
2011年に発生した東日本大震災で、日本の企業は、サプライチェーンのすそ野の広さを痛感します。
取引先の工場の稼働停止、物流の寸断などにより調達品が長期にわたり納入されない事態となりました。
東日本大震災直後、当時の調達資材購買部門が苦労したことは以下のことでした。
・調達品の製造場所を調査し報告
・調達品の工場に加え、その先の二次外注先や原材料メーカーの被害確認が必要
・被害にあわれた取引先に対しても納期を確認しなければいけない
・金曜に地震が発生したため、土日での対応
調達品の製造場所を調査し報告
当時は、多くの企業が自社の調達品がどこで生産されているかを把握していませんでした。
その結果、全ての調達品の製造場所を一から調べようとする取引先からの問い合わせが殺到します。
資材購買部門は、調達品の在庫や製造場所を調査し、自社製品への影響有無をいち早く確認することからスタートしました。
調達品の工場に加え、その先の二次外注先や原材料メーカーの被害確認が必要
調達先の工場が問題無くても、その先の部材で影響が出てモノ作りが出来ないことが多々発生した結果、二次外注先・原料メーカの被害確認が必要でした。
当時は混乱の極みにあり、情報が錯綜していました。
自社のモノつくりに問題がなくても、取引先や得意先の状況確認に加え、今まで全く関係のない企業からの問い合わせも多くありました。
なかでも一番節操がなかったのがトヨタグループなどの大手でしたね。
2次外注先の情報だけでなく、素材、さらにその先の工場の情報まで開示要求がきましたが、当時は把握している企業は少なく、資料の作成と状況の確認に追われました。
感情的な問い合わせも多々あり、失礼な電話も多く受けましたし、人の本性の醜さを感じられた場面でした。
被害にあわれた取引先に対しても納期を確認しなければいけない
一番つらかったことが、被害に合われた取引先の方に納期フォローをしなければいけなかったことです。
取引先の方にとっては、ご自身の生活も影響が出ており納期なんて二の次の状態でしょう。
にも関わらず、仕事とはいえ「いつ納入されるのか」を確認しなければならないことは、人の感情として、とてもつらいことです。
本物の有事の場合は、企業の本性が出ますよ。
普段から友好的に接していても、有事の際にひどい態度をとってしまい信頼が損なわれることがあります。
資材マンは常に冷静に対応することが必要
教訓があるとすれば、感情的な相手に対して「あいまいな態度をとらない」「できないことはできないとはっきりという」ということです。
当時のわたしの場合は、確認もせずに、適当に回答していました。
正直なところ、真面目に調査したところで、どうしようもないものはどうしようもないですから、時間の無駄を省いた形です。
タイの洪水
東日本大震災の2011年、同年に起きたタイで発生した洪水の災害においても、日本のサプライチェーンに大きな影響がありました。
当時、日本の電機・車載部品の製造業の多くが、タイでモノ作りを行っていましたが、洪水で日本企業が多く進出していた工業団地が水につかりました。
調達資材購買部員は、日本国内だけではなく、海外のサプライチェーンまで調査を行うことになります。
海外のサプライチェーンの調査で大変なことは2つ
・土地勘がない
・現地の情報が入らない
タイ洪水のときは、日本の商社窓口からの情報収集が可能でしたが、これが、さらに遠いヨーロッパや、商社を省いた直接取引の場合は、さらに言葉や時差の問題で苦労が増すことが予想できます。
調達/購買でのBCPの取り組みとは
調達・購買部でのBCPとは、調達品の供給が滞らないように事前に対策を打つことです。
具体的には、取引先のA社でトラブルが発生し供給が滞るケースを事前に想定し、以下の行動計画を作成しておきます。
・事前にA社以外に複数の調査先を確保しておく
・複数社供給ができない場合は戦略在庫を保有する
供給が滞るリスクは以下のものを想定します
・地震・火事・洪水などの天災による工場の稼働停止
・大雨・大雪などで物流が止まることでの出荷停止
・設備故障・点検による工場の稼働停止
・取引先の突然の倒産による生産停止
・貿易リスク
2011年からは、調達/資材部門でのBCPの事前準備として以下の5点が奨励されるようになってきています。
・調達品の生産場所調査
・マルチサプライヤー(複数社認定)
・マルチファブ(複数工場認定)
・戦略的在庫保有
・リスク管理の仕組み化
具体的に一つずつ解説していきます。
調達品の生産場所調査(サプライチェーンリスト)
災害があった時に一番苦労する点が、「調達品の生産場所」を知ることです。災害が起きてから調べては遅いので、東日本大震災・タイの洪水以降、各製造メーカーは調達品の生産場所調査を進めております。
調査は可能であれば、2~3次までさかのぼり行います。主要な調達品については知っておいた方が後々便利です。しかし、二次外注先の情報は場合によっては取引先が開示しない場合もありますので、注意しましょう。
全ての部材でサプライチェーンを遡ることは不可能ですので、基本的には主要な範囲で重みづけをした調査となります。
マルチサプライヤー(複数購買先認定制度)
規格品など、同じモノを複数の会社が製造している場合は、複数の製造会社を認定することがBCP対策として重要です。
仮にA社のネジしか社内の製造で使えない=認定されていない場合、A社に何かあった時、供給が停止しますが、B社を認定していた場合は、B社へ手配を切り替えることで、生産継続性を確保できます。
このように資材部門は設計部門と連携し、マルチサプライヤー(複数社認定)を進めることで、BCP体制を構築していきます。
マルチファブ(複数工場認定制度)
取引先が同じ部材を複数の工場で製造している場合、1つの工場だけでなく、複数の工場を認定することで、1つの工場の生産が停止しても他の工場から供給が可能となります。
複数の工場で同じものを作っているメーカーを採用することで、BCP対策となります。
また、中小企業で単独の工場しかない場合、企業同士で契約して、有事の際に他社の工作機械を使わせてもらうことで、事業継続計画とする動きも、出はじめました、
これは、最近の台風による洪水の教訓をもとにしています。
戦略的な在庫保有
一つの工場でしか製造が出来ない製品は、マルチサプライヤーやマルチファブの対策が取れません。
そこで必要になる考え方が、戦略的な在庫保有です。
戦略的在庫は、工場に何かトラブルがあって生産が停止した場合、復旧までにかかる期間を想定して、その分の在庫を保有することです。
具体的にある工場が地震で生産が止まった場合、復旧まで3ヶ月かかると見込まれるケースでは、3ヶ月+αの在庫を保有するようにします。
この戦略的在庫によって、従来の「在庫は出来る限り少ない方が良い」という考え方が一部修正されることになりました。
リスク管理の仕組み化
リスク管理を仕組み化しておくことで、実際のリスクに備えます。
実務での例をコチラの記事にまとめています。
実際は名ばかりのBCP
調達品におけるBCPの基本は「マルチサプライヤー」と「マルチファブ」です。
戦略的在庫は、企業のキャッシュフローを悪化させますので、最後の手段と心得ましょう。
そのため、われわれ、調達資材購買部門は、調達品のマルチサプライヤー/マルチファブ化を推進するのですが、なかなか全ての調達品で対策を取ることができません。
その理由は、BCPを要請しておきながら、顧客が認定作業をしないからです。
▼顧客が認定作業をしない理由
・部材の認定に、手間と期間とお金がかかる(評価が必要)
・先の客先のすそ野が広すぎて面倒くさい
・BCP対策をしても原価低減にならないことも多い
サプライヤーを新たに認定するためには、調達部材を追加で認定する必要がありますが、部材の認定に「手間と期間とお金」がかかるのが一番の難点です。
認定とは「社内の製造で使えるモノかどうかの確認・評価」を行うことです。
苦労して認定しても、あくまでバックアップ。
原価低減などの分かりやすい成果が出づらいのが難点です。
特に、認定評価を進めるのは、社内の設計部門や品質管理部門ですが、以下の課題があります。
・試作用の素材の購入LOT分の金額が負担できない
・製造部門が忙しく試作をする隙間がない
・設計・生産技術・品質管理部門の合意が得られない
しかしながら、有事の際には、調達/資材買部門の精神的ストレスはすさまじいものがあります。
優秀な調達資材購買部員は、有事の際に、自身の仕事の負荷やストレスを減らす意味でも、BCPの大義名分を利用して、BCPの評価に時間と手間をさいてくれるように、社内や顧客を誘導し、事前準備をしています。
BCP対策では、いつあるか分からない災害のために努力することが求められていますが、資材購買部門以外の直接関係ない部署は重要性を認識できません。
大義名分を掲げて、社内を動かしていくためには、自分がBCPの目的を理解していなければなりませんよね。
BCPの問題点:実態は親会社の自己満足調査
最近の傾向として、「パートナー様との協力関係」「調達管理対応」という心地よい名のもとに、サプライヤーへの押し付け・企業情報の抜き取りを行う会社が増えています。
本来の評価・認定作業を行わずに、小手先の調査で満足する親会社が多いです。
・サプライチェーン調査
・部品品番ごとのメーカー名・原産国・生産状況を年次で報告
・有事の際の報告を10時間以内にメール配信
・フォーマットが顧客指定
いわば、保険(保身)です。調査しておいても問題が解決するはずがないのに、手を打っている安心感が欲しいようです。中小の下請け企業にとっては負担なことばかりで、われわれからすれば
というのが本音。
大手の会社は人が余っているので、おかしな「押しつけ」をしてきます。
このような、原価が上がる無駄な仕事ばかりしていると、海外企業に負けますね。
解決策としては、下記の手を打っておきます。
・力のある得意先側でに在庫を持っていただく
・不安をあおって無理にでも評価をとりつける
・自社での使用評価までは終えておく
最近のBCP実施事例
古河電工 日光工場の雪害事故
栃木県日光市の伸銅品材料を製造する工場の屋根が豪雪の雪の重みで崩落し、圧延設備が使用不能になりました。
リン青銅大手 三菱電機メテックスの事業撤退
携帯電話のコネクター部分に使用されるリン青銅条を製造していた三菱電機メテックスが、事業撤退を発表。
世界中のスマホ市場の拡大に、素材製造が追いつかない事態となり、市場から、1年ほどリン青銅が枯渇しました。
熊本地震
九州地区は、日本のシリコンバレーといわれるほど、半導体関連の工場が多い地域です。
熊本県益城町を震源とする地震で、ルネサステクノロジーの半導体製造工場や、SONYのイメージセンサのラインが長期間ストップする事態となりまりました。
日中問題(政治問題)
排気ガスの触媒として重要な資源であるレアメタルの輸出を一方的に中国側が規制をかけたことで、日本の自動車産業に多きな打撃を与える事態となりました。
この事例のように、不意な政治的なリスクもBCPの対象となりえます。
台風19号での洪水被害
最近の台風19号の洪水被害では、長野近辺の中小製造業者が浸水。
トヨタの関連企業も多く存在する地域で、自動車の製造ラインが止まる事態に発展しています。
台風、地震による日本国内のリスクも想定が難しいばかりか、海外との政治的な関係、為替リスクほか、無数にリスクは存在しており、資材調達購買のBCP対応は、年々、複雑になってきています。
まとめ(未来予想)│これからBCP対応が必要になるもの
2011年の東日本大震災以降、調達資材購買部門にとって、BCPは必須となりました。
調達資材購買部門で働く人は、自社の調達品の製造場所や、BCPの対策ができているか?を確認していく必要があります。
一方で、BCP対策は、直接の利益につながらない仕事です。
苦労だけが多く感じられるため、苦痛を感じることも多いでしょう。
しかし、BCPを通じて得られる知識(他社で同じものを作っているか、製造場所はどこか)は、資材部員としての付加価値を高めることになります。
BCPを意識しながら業務をしていくと、万が一があった時に、きっと役に立ちます。
BCPは、いざというときに「あなたが楽に対応することできる保険」であり、「自身のスキルを上げるツール」と割り切って取り組むことで、モチベーション高く保つことができますよ。
未来予想:これから入手困難になるもの
最後に、今後必ず入手困難になるものを提示します。
賢いあなたは今のうちにBCPを策定して備えましょう。
・半導体
・樹脂材料
・木材
・銅素材
考えるヒントは以下の3つの流れです。
①米中関係
②車のEV化と自動運転
③5G社会の到来
①米中関係
米中摩擦が起きると、これまで中国から輸入していた木材、米国から調達していた樹脂素材の入手が厳しくなる事が予想されます。
樹脂材料は、3Dプリンターが一般化される2030年ごろには最も入手が難しい資材になるかもしれません。
②車のEV化と自動運転
車のEV化が起きれば、電気を伝達する真鍮や純銅系の素材が枯渇します。
特に、純銅系の素材は製造メーカーが限られる上に、電気銅を供給できるメーカーが少ないので、需要に供給が追いつかない自体が予想できますよ。
EV化の波は2023年ごろにピークが予想されますので、そこまで銅系の金属材料を調達しているバイヤーの皆様は、海外(特に中国、ヨーロッパ)からの調達を検討しておくべきですね。
③5G社会の到来
車の自動運転や5G社会の到来はデジタル化を促進していきます。
デジタル処理に必要な半導体の供給体制はまだまだ弱いので、世界的な半導体不足が懸念されます。
特にパソコンやスマホ向けに供給されていた半導体を車メーカーが奪いに来る形になるでしょう。
半導体製造メーカーも、車向けの供給を想定していないので、カンバン方式(ジャストインタイム)に対応した短納期対応ができません。
なので、半導体不足はカーメーカーの製造ラインをも止める事態となるでしょう。
上記のような状況になったときに、何も対策をしていない資材調達担当は、ノイローゼ寸前まで追い込まれるかもしれません。
無駄なストレスを抱えたくないなら、今のうちからBCP対策をしておきましょう!
今回は以上です。